Dental Implants a Short Summary
- Admin
- Jun 2
- 10 min read

What is a Dental Implant?
A dental implant is a small, screw-shaped post typically made of titanium or ceramic, designed to replace the root of a missing tooth. Once placed into the jawbone, it undergoes a natural process called osseointegration, where the bone fuses with the implant, providing a stable foundation for a crown, bridge, or denture. This process ensures durability and a natural feel, closely mimicking a real tooth.
There are different types of implants available, with variations in design, material, and size to accommodate various clinical situations. These are commonly used to restore both aesthetics and function, enhancing chewing ability and preserving jawbone integrity.
Unlike dentures, which rest on the gums, implants are embedded into the bone, offering superior stability. The success of an implant relies on factors such as the patient’s bone quality, the surgeon’s expertise, and the implant brand used.
Implants can be an excellent long-term solution for tooth loss, especially when high-quality materials and proper manufacturing processes are involved. With a wide selection of implant manufacturers worldwide, patients can choose options ranging from Swiss, German, and Israeli, to Korean and Brazilian brands—each known for distinct innovations and standards.
Ultimately, when considering implant treatment, you should trust your healthcare provider to recommend the best implant tailored to your needs. It's also essential to select a provider that guarantees aftercare, which ensures all follow-up treatment happens conveniently in your home country.
Dental Implant Treatment Duration
The duration of a dental implant procedure can vary based on individual health conditions, the complexity of the case, and the type of implant system used. However, most treatments follow a two-stage process with a total healing and integration time spanning several months.
The first stage involves the surgical placement of the implant into the jawbone. After this, a 3-month healing period is typically recommended to allow for osseointegration—the critical phase where the bone bonds with the implant. This stage is crucial for ensuring long-term stability and preventing complications.
Once healing is confirmed, the second stage begins with the attachment of the abutment, a small connector piece that supports the final crown or prosthesis. Depending on the clinical approach and implant type, some cases may allow immediate loading, reducing the overall duration of treatment.
Some implant brands have refined their manufacturing processes and surface treatments—such as acid etching and sandblasting—to accelerate healing and enhance integration. These advancements help reduce waiting times while maintaining excellent success rates.
Dental Implant Parts: Abutment
One of the key components of a dental implant system is the abutment—a small but essential part that connects the implant post to the visible crown or bridge. Acting as a transitional element, it ensures that the prosthetic tooth is securely anchored and properly aligned.
Abutments come in a variety of materials, primarily titanium, ceramic, and occasionally zirconia. The choice of material is influenced by factors such as aesthetics, tissue compatibility, and the location of the implant. For instance, ceramic and zirconia abutments are often chosen for front teeth due to their natural appearance and translucency.
There are also two main types of abutments: prefabricated and custom-made. Custom abutments are crafted using advanced CNC milling techniques, allowing for a precise fit that matches the unique contours of a patient’s gums and bone structure. These custom solutions contribute significantly to both function and cosmetic outcomes.
The abutment must be both sterile and highly precise, fitting the implant post at micron levels. High-end implant manufacturers maintain strict quality control protocols using microscopes and vision devices to verify exact specifications before packaging.
Titanium Grades
When it comes to dental implants, titanium is the gold standard. But not all titanium is created equal. The most commonly used grades in implant dentistry are Grade 4 and Grade 5, each offering distinct properties suited to different clinical needs.
Grade 4 titanium is commercially pure and offers excellent corrosion resistance, making it ideal for long-term biocompatibility. Its slightly lower strength is balanced by superior osseointegration, allowing the bone to fuse effectively with the implant surface.
On the other hand, Grade 5 titanium—also known as Ti-6Al-4V—is an alloy combining aluminium and vanadium for enhanced strength. It’s widely used in more demanding cases where mechanical durability is paramount, such as in patients with higher bite forces or those needing smaller-diameter implants.
Top implant manufacturers ensure their titanium meets stringent international standards, undergoing thorough quality control and ultrasonic cleaning processes to remove impurities. These steps are vital to maintain the material’s integrity and ensure successful integration with the jawbone.
Brands associated with Swiss, German, and Israeli engineering often highlight their use of high-grade titanium, offering confidence in both performance and longevity. By choosing a trusted provider patients benefit from implants crafted with premium materials.
Also note that, titanium is completely biocompatible and used for decades. Titanium allergy is a really low probability 6 out of thousand implant patients might have it. To be sure, you can get MELISA test before getting dental implants to see if you have an allergy.
How is it produced?
The production of a dental implant involves an intricate blend of advanced engineering and medical precision. Each step is crucial, from material selection to the final packaging, ensuring the implant’s safety, durability, and biocompatibility.
It all begins with selecting medical-grade titanium—either Grade 4 or Grade 5—or sometimes ceramic or zirconia, depending on the implant design. The raw material is then processed through CNC milling, a high-precision computer-controlled technique that shapes the implant into its intended form with tolerances at micron levels.
Post-milling, the implants undergo various surface treatments to enhance osseointegration. These include acid etching and sandblasting with controlled sand sizes. This increases surface roughness, encouraging the bone to bond more effectively with the implant.
After shaping and surface treatment, implants are subjected to a rigorous washing and cleaning regime. Ultrasonic cleaning and rinsing with purified acids help remove any residues from manufacturing.
The next step is sterilisation—often achieved with gamma radiation—followed by secure packaging in a sterile environment. At every stage, quality control checks are implemented using microscopes and vision devices to ensure the product meets international standards.
Whether the implant originates from Swiss, German, Korean, American or Brazilian manufacturers, the underlying goal is the same: to create a precise, clean, and safe implant.
Milling
Milling is a cornerstone process in the production of high-quality dental implants. Using CNC (Computer Numerical Control) milling, manufacturers achieve exceptional precision, sculpting implants from solid rods of titanium, zirconia, or other biocompatible materials.
This technique allows for intricate shaping at micron levels, ensuring the final product fits perfectly into the bone and integrates seamlessly with the surrounding tissues. The precision achieved during milling is critical—not just for the implant’s fit but for the long-term success of the implant treatment.
Modern milling systems rely on vision devices and in-line inspection tools to continuously monitor accuracy. These systems verify every cut and angle, minimising deviations and enhancing quality control. As a result, implants exhibit consistent performance and compatibility with prosthetic components like abutments.
Premium implant manufacturers, especially those from Swiss, German, and Israeli origins, often invest in state-of-the-art milling technologies to produce implants with superior geometry and finish.
Choosing implants manufactured using high-end CNC milling ensures not just structural integrity but peace of mind—because every curve, thread, and detail has been engineered for excellence.
Washing and Cleaning
After the milling process, dental implants must undergo rigorous washing and cleaning to eliminate any microscopic debris, oil residues, or contaminants that could interfere with osseointegration or pose a risk to patient health.
The cleaning protocol often starts with ultrasonic cleaning, where high-frequency sound waves agitate a cleaning solution to reach even the tiniest crevices of the implant. This technique dislodges contaminants without damaging the implant’s intricate surfaces.
Following this, the implant is typically treated with purified acids in a carefully controlled sequence. These acids further strip away residues and prepare the surface for subsequent treatments, such as sandblasting or sterilisation.
Leading implant manufacturers use automated cleaning stations and sterile environments to maintain consistency and minimise human error. These procedures are especially prevalent in Swiss and German facilities known for their precision and attention to detail. Vision devices and microscopes are employed during inspection to ensure the implant meets stringent cleanliness standards before moving to the next production phase.
Sandblasting
Sandblasting is a crucial step in the surface treatment of dental implants, designed to improve the implant’s ability to bond with bone through enhanced osseointegration. During this process, the implant is bombarded with fine sand particles at high speed, creating a roughened surface texture that encourages better tissue adhesion.
Different implant manufacturers use varying sand sizes—typically in the micron range—to achieve specific surface characteristics. The choice of sand grain size and blasting pressure must be carefully calibrated to avoid compromising the structural integrity of the implant while optimising biological response.
Often paired with acid etching, sandblasting increases the surface area of the implant, allowing bone cells to attach more effectively. This dual approach is known to shorten the healing period and improve long-term stability, making it a preferred technique among Swiss, German, and Israeli manufacturers renowned for innovation.
The process is carried out in a sterile environment, followed by thorough ultrasonic cleaning to remove any residual particles. Quality control measures, including the use of microscopes and vision devices, ensure that each implant meets strict specifications before packaging.
Surface Treatment
Surface treatment plays a vital role in determining the biological success of a dental implant. It directly influences how the bone reacts to and bonds with the implant—a process known as osseointegration.
After sandblasting, most implants undergo acid etching. This involves immersing the implant in a mixture of acids that further roughen the surface on a microscopic level. The resulting micro-pits provide an ideal environment for bone cells to anchor, strengthening the implant-bone interface.
Some implant manufacturers incorporate additional proprietary techniques—such as plasma spraying or chemical modifications—to enhance surface bioactivity. These treatments vary depending on the implant's type, material (e.g., titanium, ceramic, or zirconia), and the manufacturer’s innovation standards.
The effectiveness of a surface treatment can influence the overall duration of the healing process. A well-treated implant surface can reduce the 3 month healing time typically required, allowing patients to receive their final restoration sooner.
Facilities in Swiss, Korean, Israeli, and Brazilian implant production centres are often recognised for their sophisticated surface technologies. Their precision-driven manufacturing processes ensure consistency, safety, and compatibility across product lines.
Cleaning and Sterilization
Following surface treatment, thorough cleaning and sterilization is essential to prepare the dental implant for safe clinical use. This stage ensures that no contaminants, bacteria, or residual materials remain on the implant that could hinder osseointegration or trigger adverse reactions.
The cleaning process begins with ultrasonic cleaning, which uses high-frequency vibrations to dislodge any remaining particles from surface treatments like sandblasting or acid etching. This is followed by multiple rinsing stages using medical-grade solutions and purified acids, designed to achieve a state of surgical cleanliness.
Sterilisation is then carried out using high-efficiency methods such as gamma radiation or ethylene oxide gas. These techniques ensure the complete eradication of microbes without compromising the structural or surface integrity of the implant.
Once sterilised, the implants are sealed in sterile packaging within controlled cleanroom environments. Top implant manufacturers—especially those from German, Swiss, and Korean backgrounds—maintain rigorous quality control during this phase, employing microscopes and vision devices to ensure every implant meets exacting safety and hygiene standards.
Quality Control at Each Step
The success of a dental implant depends heavily on the quality control exercised throughout its production. Every stage—from raw material selection to final packaging—is governed by stringent protocols to ensure precision, safety, and reliability.
Starting with CNC milling, manufacturers monitor each implant’s dimensions at micron levels using vision devices and microscopes. This ensures structural accuracy and consistency across batches. Next, after processes like sandblasting, acid etching, and ultrasonic cleaning, implants are examined for surface uniformity, cleanliness, and material integrity.
Sterilisation, often via gamma radiation, is followed by a final inspection before implants are sealed in sterile packaging. Swiss, German, Israeli, and Brazilian manufacturers are renowned for their commitment to quality, often incorporating multi-tiered inspection systems to double-check each product before it leaves the facility.
In the case of implant brands that take shortcuts on quality control, patients risk complications such as poor osseointegration, infection, or implant failure. That’s why selecting a provider who values excellence is crucial.
Swiss Implants or German Implants?
When choosing a dental implant, many patients and professionals debate between Swiss and German implants—two of the most respected origins in the implant industry. Both countries boast world-class engineering, stringent quality control, and a long history of innovation in implant manufacturing.
Please do not forget that there hundreds of Swiss and German manufacturers each different from each other by quality, price, and designs. Here the general views from the past is argued.
Swiss implants are renowned for their ultra-precise CNC milling, meticulous surface treatments, and advanced vision device inspections. Swiss companies often lead in cutting-edge techniques like laser micro-texturing and custom abutment solutions. These features contribute to outstanding osseointegration and aesthetic results.
On the other hand, German implants are praised for their robust design, excellent titanium purity—often Grade 4 or Grade 5—and systematic quality assurance protocols. German manufacturers frequently focus on durability and biomechanical strength, making their implants ideal for complex or load-bearing cases.
While both are exceptional, the choice may depend on clinical needs, patient preferences, and treatment goals. For instance, Swiss systems may suit aesthetic zones requiring high precision, whereas German implants may be preferable in demanding, high-stress environments. However, this is just a generalization and every origin of a country can have great implants.
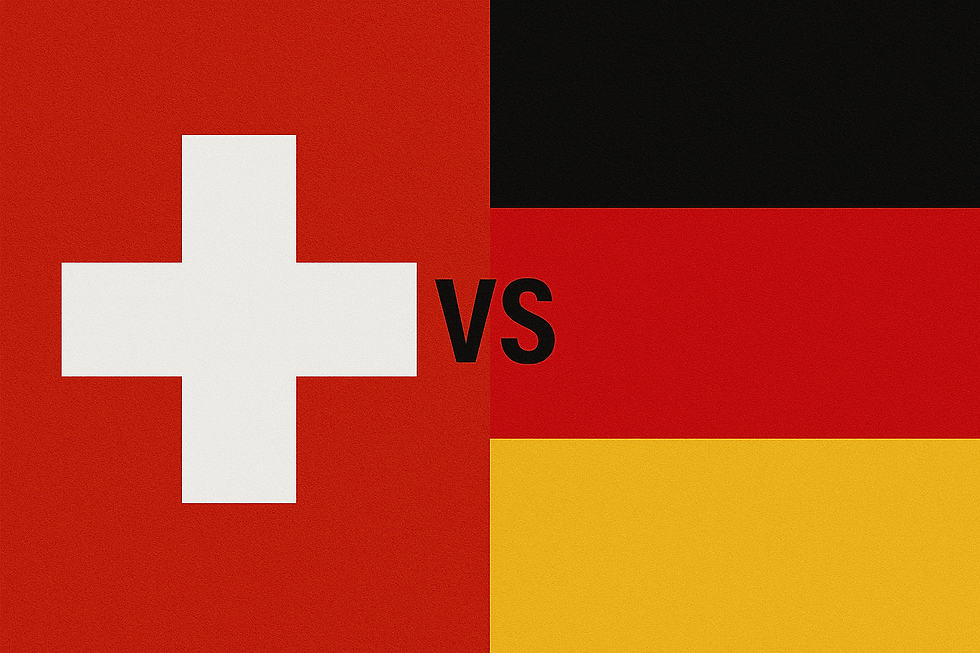
Which Implant Should I Get?
Choosing the right dental implant involves more than selecting a reputable brand—it’s about finding a system that aligns with your clinical needs, aesthetic expectations, and long-term health. With numerous implant manufacturers offering a wide variety of types, materials, and designs, making an informed decision is crucial.
Top-tier brands from Swiss, German, Israeli, Korean, and Brazilian origins all offer exceptional quality. The choice often comes down to specific features: ceramic for aesthetics, titanium Grade 4 or Grade 5 for durability, and advanced surface treatments like acid etching and sandblasting to promote quicker osseointegration.
Equally important is the provider you choose. The best implant is only as effective as the team placing it and the support you receive afterward. That’s why you should trust your healthcare provider—especially one that ensures continuity of care.
Comments